In recent years, PERC solar cell technology (from the English. Passivated Emitter Rear Cell) has become one of the favorites of research and development in the photovoltaic industry. Today it is considered one of the top advanced technologies in the production of high-performance solar panels .
What is PERC
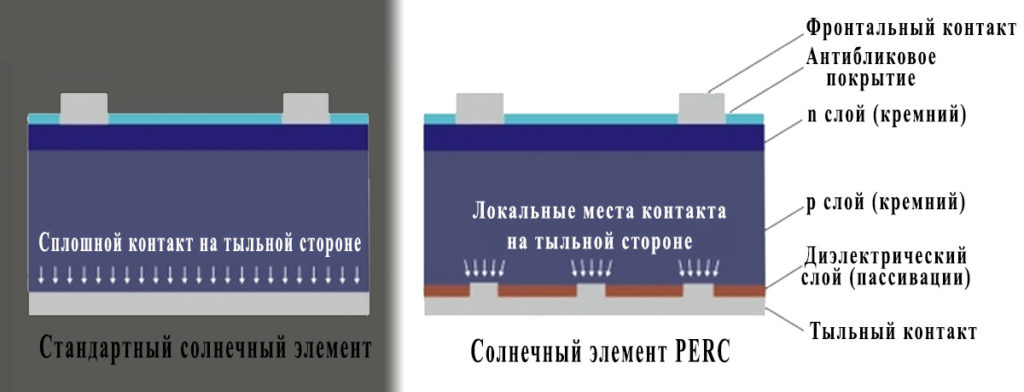
The production of photovoltaic cells has been dominated for many years by one Al-BSF modular technology with an aluminum backing . However, it is close to its practical limit, and further improvement in efficiency is unlikely. This is because for many years, manufacturers have focused on developing innovations for the front side of the solar cell, not paying due attention to its reverse side. The search for solutions to improve efficiency has prompted the solar industry to use passive emitter rear contact (PERC) solar cells. In fact, PERC technology has become a procedure for improving standard Al-BSF photovoltaic cells. The PERC photocells provided access to the module with a higher power rating, for example up to 370W for a 72 cell module.
The abbreviation PERC stands for emitter back contact passivation (literally, passivated emitter and rear cell/module). The main feature of solar panels with PERC technology is that a dielectric layer is located on the reverse side of the module. It reflects the light rays that have passed through the photocell and redirects them back inside the silicon layers. This generates more electricity. This process is otherwise known as backside passivation. PERC technology helps to increase the spectral sensitivity of photovoltaic cells, which is achieved due to the ability to absorb a larger amount of sunlight.
PERC technology was developed in 1980 in Australia by a group of scientists led by the director of the Australian Center for Advanced Photovoltaics at UNSW (University of New South Wales), Professor Martin Green, but it began to be actively used only 5–6 years ago.
Due to its merits, in the last two or three years, PERC technology has become a priority for manufacturers of both poly- and monocrystalline panels.
How PERC technology works
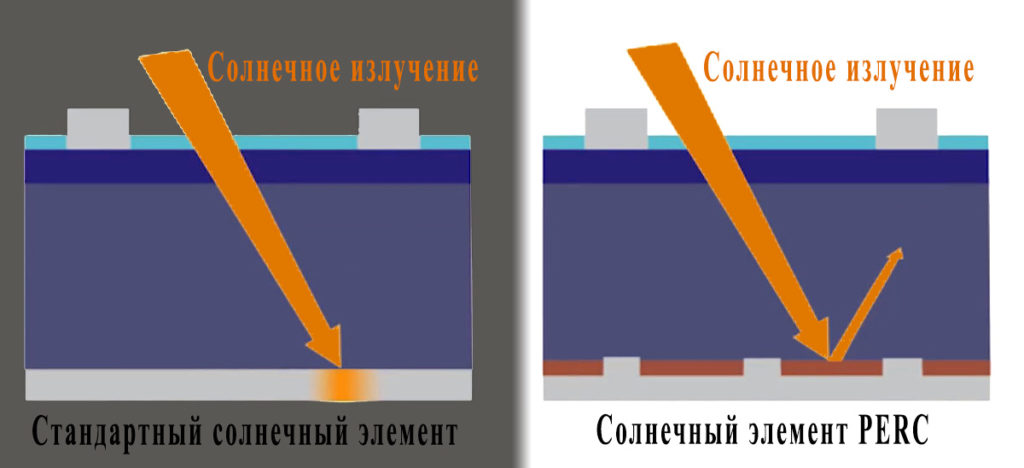
Compared to traditional panels, modules with PERC technology have higher performance. Using this innovation is a good way to increase the reflectivity of the back surface of a solar cell by increasing the number of photons that can be absorbed and converted into more electricity produced.
Photoelectronic emission is a rather complicated process. The power generator in photomodules consists of two parts: a base and an emitter with a pn contact zone – the boundary between them. It is here, at the boundary section of the transition, that an electric current is generated, the electrons rush to the emitter. A similar scheme for the production of electrical energy is used in PERC modules.
The task of solar panels is to produce electric current, and the principle of its production is as follows. Photons (particles of light) seem to “knock out” electrons (negative particles) from the silicon layer. Both those and other particles have the property of “wandering”. In order for an electric current to be generated, an electron “knocked out” of silicon must reach the contact boundary. But, as a rule, most of the negative particles (electrons) simply settle in the lower layer of the base. That is why the efficiency of modern solar panels does not exceed 20%.
If we compare a traditional solar cell and a panel with PERC technology, then in the first case, the rear contactor is a thin layer of aluminum that acts as a continuous current collector, and in the second case, PERC photocells use a layer of aluminum with sputtering and laser perforation. Thus, in the additional layer there are numerous microholes through which electrons escape. Due to the dielectric properties of the back layer in PERC photovoltaic cells, the electrons that settle at the bottom are again redirected until they find a hole in the perforation in order to go to the emitter.
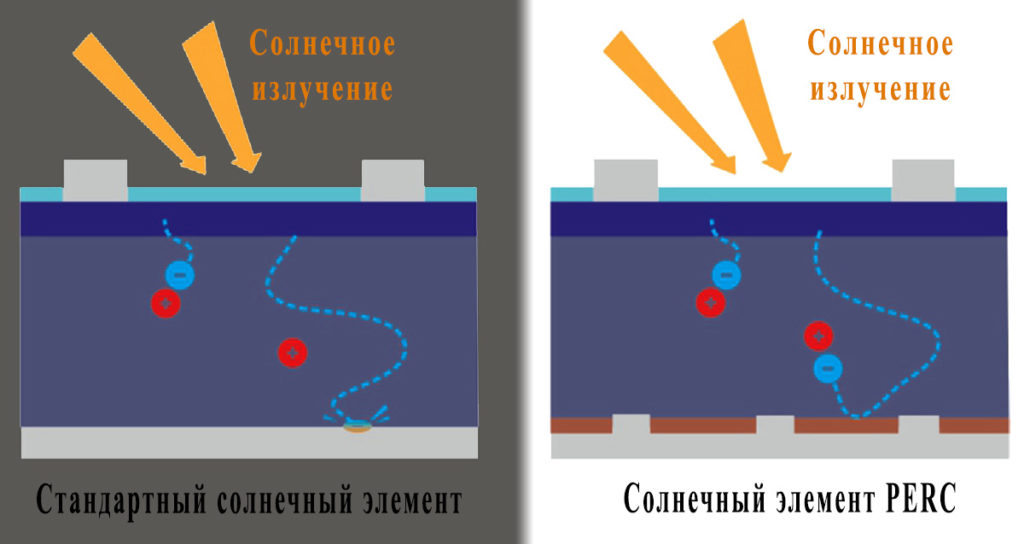
In fact, an additional dielectric passivating layer reduces the recombination of electrons (the process of the disappearance of a pair of particles – free carriers of the opposite charge to any medium with the release of energy). In other words, this means the tendency for electrons to recombine and basically block electrons from wandering freely through the solar cell, causing it to fail to reach its potential efficiency. In the case of using an additional dielectric layer, the electrons generated near the back of the PV module can freely move up to the emitter and contribute to the increase in electric current generation, which means that the efficiency of the solar panel with PERC technology is increased.
The additional dielectric passivation layer can reflect wavelengths above 1180 nanometers outside of the photocell, which normally generates heat. In standard photomodules, such wavelengths are easily absorbed by the back of the metallized side of the photocell and transformed into heat, which reduces the efficiency of solar panels. By reflecting wavelengths above 1180 nanometers, the dielectric passivation layer in PERC modules helps the PV cell operate more efficiently without overheating.
Several other types of PERC photovoltaic cells have also been developed, such as PERL (passivated rear emitter, locally scattered) and PERT (passivated rear emitter, fully diffused). However, they are not yet widely used.
Benefits of PERC Technology
When it comes to research and development in the solar energy industry, there are two main goals that manufacturers and consumers strive to achieve: cost reduction and efficiency improvement . Solar cells with PERC technology have an efficiency of over 20-22%+, while standard solar cells average around 18-19%. For example, improving the efficiency of photovoltaic cells due to PERC technology leads to an increase in power by 3-5 W for a single crystal module. with 60 elements.
Among the main advantages of PERC modules are the following.
- PERC technology can be used in both mono- and polycrystalline panels.
- The use of PERC technology increases the efficiency of solar modules by up to 25% due to an increase in the absorbing capacity of the photocell, reducing unwanted overheating in it, reflecting already generated electrons into the pn junction zone, which is recognized as one of the highest values in the industry.
- The production of photovoltaic modules using PERC technology is very different from the production of conventional photovoltaic cells, since only the back surface is modified by simply adding a dielectric layer and using lasers for holes (perforations). Thus, the installation of some special complex equipment is not required, it is enough to modernize existing production lines. That is, solar panels with PERC technology have a higher power output with minimal investment and few risks.
- When operating PV cells with PERC technology, short circuit currents increase, resulting in an increase in current strength, which simultaneously increases the voltage and, as a result, the output power of the solar panel.
- The reflectivity of panels with PERC technology increases to 90-95% compared to 65% for panels of typical configurations.
- PERC elements perform well in high temperature or low light environments.
- Due to more attractive temperature coefficients, solar panels with PERC technology are the best solution for use in hot climates, helping to reduce heat loss. As a result, end users get maximum efficiency from their solar systems throughout the year.
- Installing solar panels with PERC technology is more cost effective than traditional solar panels. The innovation itself affects the cost of the finished solar plant insignificantly, but at the same time significantly increases its efficiency. In addition, to produce the same amount of electricity as a standard solar panel, PERC technology typically requires fewer photovoltaic cells.
Why is PERC technology chosen by solar cell and panel manufacturers?
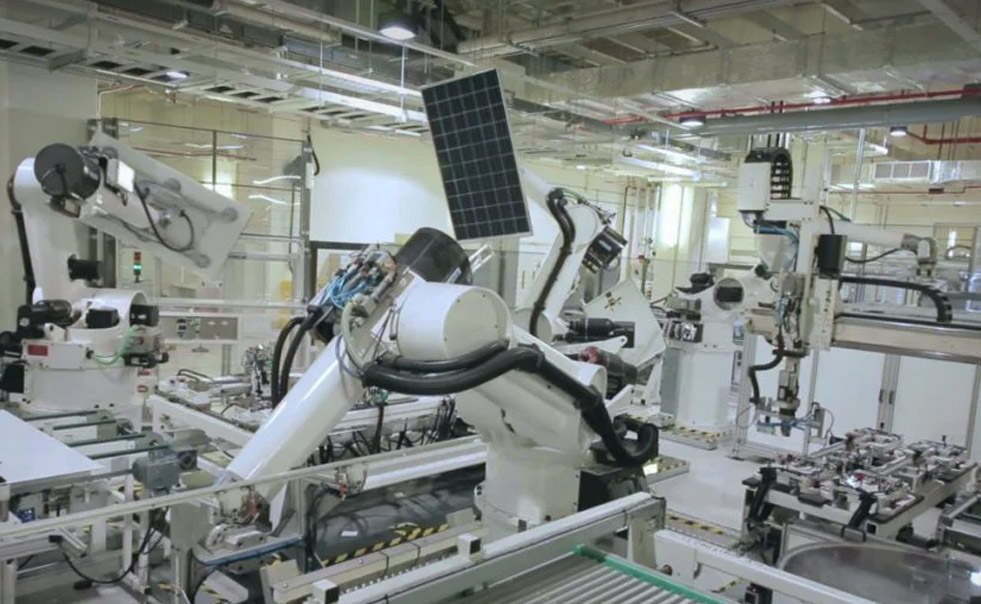
The investment to switch to a PERC production line requires minimal modifications to existing cell production lines. Manufacturers can easily transition to producing a quality and efficient product without making large capital investments to completely replace existing equipment. There is a boom in the world market in the direction of increasing the capacity for the production of modules with PERC technology. Experts predict that this process will develop rapidly over the next few years. In addition, panel manufacturers can now produce a more energy-intensive module without significantly increasing assembly costs.
Why is PERC preferred by panel engineers and installers?
Panels with PERC technology give more freedom to panel installers, especially when it comes to spaces or places that were previously considered insufficient for solar installations. PERC panels have a higher energy density per square meter. m and work well in low light and high temperatures. Clearly, when generating power, PERC panels are superior to standard counterparts. Solar designers can use fewer panels to achieve overall “output” energy goals when their footprint is limited. Also, panels with PERC technology without loss of efficiency can be installed in places and spaces that were previously considered unsuitable for solar energy facilities. This allows engineers and installers to be more flexible and better able to adapt to project goals.
Why is PERC technology cost effective?
Since the production of panels with PERC technology is not radically different from the production of standard panels, the risk of investment, which is often associated with any know-how, is reduced. Using proven technology and modifying standard panels, there is virtually no risk that the introduction of PERC technology will drastically change the structure and interior of the photocell. That is, the funds will not be “thrown to the wind.”
The ultimate goal of PERC panel manufacturing is to provide a reliable and cost-effective way to generate energy for residential, commercial and utility projects. When using solar panels with PERC technology, the total electricity generation over the lifetime of the entire solar plant is increased without a significant increase in cost per watt.
Why will PERC be the dominant solar cell technology?
The prospects for PERC modules seem promising, and the current level of scientific and technological progress makes it possible to put the production of such solar panels on the conveyor. Today, many recognized brands of solar panels have already introduced PERC technology into production. Among them are Canadian Solar, LG, REC Solar, Winaico, Trina Solar, Jinko Solar, Solar World, etc.
PERC technology will dominate in the coming years, not only due to its advantages, but mainly because it does not require a complete retooling of production. For example, manufacturers can easily upgrade existing production lines because PERC is compatible with existing screen printing equipment. And there are many such engineering solutions.
According to experts, in the coming years, solar panels with PERC technology will be much more attractive in price for the mass consumer than traditional solar panels. But so far, such photomodules (PERC) are an order of magnitude more expensive than standard counterparts. A significant price reduction can be seen only against the backdrop of mass production and the increasing popularization of PERC technology. Therefore, already now, understanding the prospects and advantages of such solar panels, an increasing number of solar panel manufacturers are rebuilding their production facilities to introduce PERC technology.